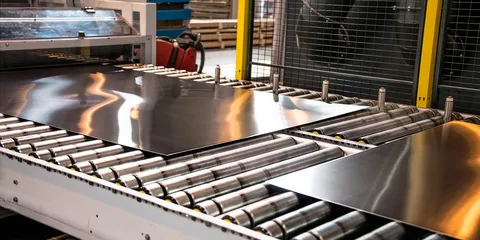
In the modern manufacturing world, sheet metal processing plays a crucial role in producing high-quality products that meet specific design requirements. By employing advanced sheet metal processing techniques, businesses can increase their production efficiency while reducing waste and energy consumption. The latest technologies and innovations in this field have opened up a wide range of possibilities, making it essential for manufacturers to keep up with these advancements. In this article, we will explore the best techniques to maximize efficiency in sheet metal processing.
Automation in Sheet Metal Processing
Automation has revolutionized the sheet metal processing industry, improving speed, accuracy, and consistency. With automated systems in place, the need for manual labor has significantly decreased, reducing human error and increasing production output. Automated machinery, such as robotic arms and CNC (Computer Numerical Control) machines, can perform tasks like cutting, punching, bending, and welding with exceptional precision. These systems not only speed up operations but also minimize material waste by ensuring cuts are made efficiently and accurately.
Moreover, automation in sheet metal processing reduces the need for on-site supervision, freeing up valuable time for operators to focus on other aspects of production. The integration of sensors and AI-driven software allows real-time monitoring of the manufacturing process, which enables adjustments to be made instantly, preventing potential issues before they escalate. By investing in automation, manufacturers can significantly boost their productivity while ensuring the highest quality standards are maintained across all production stages.
Laser Cutting Technology
Laser cutting technology has become one of the most widely used advanced techniques in sheet metal processing due to its accuracy, speed, and versatility. Laser cutters utilize focused beams of light to cut through metal sheets, offering high precision with minimal heat distortion. Unlike traditional cutting methods, laser cutting can achieve intricate designs with tight tolerances, making it ideal for producing parts with complex geometries. This technology also reduces material waste since it creates cleaner cuts with fewer burrs and edges that require post-processing.
In addition to precision, laser cutting offers greater flexibility compared to other methods. It can cut various types of metals, including stainless steel, aluminum, and titanium, and is effective for both thin and thick sheets. Furthermore, laser cutting can be used for other processes, such as engraving, marking, and welding, increasing its versatility across different industries. As the demand for high-quality, customized sheet metal parts continues to grow, laser cutting will remain a vital tool for manufacturers aiming to stay competitive and efficient in their operations.
Advanced Bending and Forming Techniques
Bending and forming are essential processes in sheet metal processing, enabling the creation of shapes and structures that are fundamental to many products. Traditional bending methods, like press brakes, are still widely used, but recent advancements have led to more efficient and precise techniques. One such innovation is the use of robotic bending systems, which automate the process, enhancing consistency and minimizing the potential for human error. These systems are equipped with high-end sensors that ensure the correct angle and positioning are achieved for each piece.
Additionally, newer bending technologies, such as air bending and bottoming, offer better control over the sheet metal’s final shape, reducing the likelihood of defects and material waste. Precision and flexibility are key benefits of these advanced bending techniques, as they allow manufacturers to create intricate shapes with varying thicknesses and complex geometries. These modern systems not only improve product quality but also streamline the production process, resulting in faster turnaround times and cost savings in the long run.
Water Jet Cutting for Precision and Clean Edges
Water jet cutting is another advanced sheet metal processing technique that offers several benefits, particularly when it comes to producing clean, precise cuts without heat distortion. Water jet cutters use a high-pressure stream of water mixed with abrasive particles to slice through metals with extreme precision. One of the key advantages of this method is that it does not produce heat, eliminating the risk of warping or thermal damage to the metal. As a result, parts maintain their structural integrity and finish, even when working with heat-sensitive materials like aluminum or copper.
This technique is particularly beneficial when cutting intricate designs and thicker materials, which may be difficult to achieve with traditional methods. Water jet cutting also allows for minimal material wastage, as the cuts are more accurate and require less post-processing. Moreover, since it does not rely on heat, it produces no fumes or harmful emissions, making it an environmentally friendly option. As industries demand higher quality and more sustainable practices, water jet cutting is becoming an essential method in advanced sheet metal processing.
Additive Manufacturing in Sheet Metal Processing
Additive manufacturing, also known as 3D printing, is making waves in the sheet metal processing industry as it offers new ways to design and produce parts with intricate geometries. While additive manufacturing is typically associated with plastic and resin-based products, recent advancements have enabled its application in metalworking as well. Using metal powders and lasers, additive manufacturing can build complex metal parts layer by layer, offering complete design freedom and minimizing material waste.
This technology is especially valuable in situations where traditional manufacturing methods may be impractical due to the complexity or size of the parts. For example, additive manufacturing allows for the creation of customized metal components that would be too costly or difficult to produce using conventional methods. In addition, it facilitates rapid prototyping and on-demand production, reducing the time from design to final product. As additive manufacturing continues to evolve, it has the potential to revolutionize the way sheet metal parts are designed and produced, providing manufacturers with unparalleled flexibility and efficiency.
Conclusion
Incorporating advanced sheet metal processing techniques into manufacturing operations can significantly enhance efficiency, quality, and sustainability. Automation, laser cutting, advanced bending, water jet cutting, and additive manufacturing are just a few examples of how modern technologies are transforming the industry. By embracing these innovations, manufacturers can streamline their processes, reduce waste, and maintain high standards of precision, ultimately staying ahead of the competition in an ever-evolving marketplace. As these technologies continue to develop, the potential for even greater advancements in sheet metal processing is immense, offering new opportunities for businesses to improve their operations and achieve long-term success.